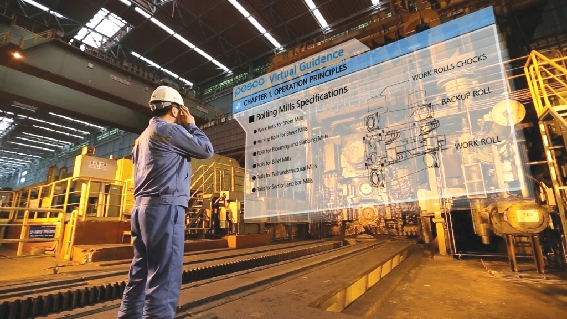
30일 재계에 따르면 포스코는 철강 연속 공정 특성을 반영해 개발한 스마트팩토리 플랫폼 ‘포스프레임’을 올 하반기까지 7개 공장에 확대 적용하기로 했다. 7개 공장에 추가 확대 적용할 경우, 포스코는 포항·광양제철소를 통틀어 총 27개 공장에 포스프레임을 적용하게 된다.
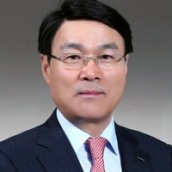
최 회장은 2018년 취임 당시 “스마트 기술을 통해 철강 경쟁력을 더욱 강화하겠다”라며, “‘스마트 포스코’로 체제 전환해 미래 50년을 준비해 나가겠다”라고 말했다.
포스프레임은 포스코가 개발한 세계 최초의 연속 제조 공정용 스마트팩토리 플랫폼이다. 이는 연속 공정이 생명인 제철소에 특화된 플랫폼이다.
포스프레임을 이용하면 여러 공장에서 발생하는 서로 다른 특성의 정보들을 한 곳에 수집해 누구나 가공할 수 있도록 데이터로 변환해 효율적인 업무가 가능하다.
포스코는 포스프레임 확대 적용을 통해 △불량 최소화 △생산 현장 최적화를 통한 원가 절감 △업무 장애 해결 및 효율적 업무체계 실현 등의 효과를 기대하고 있다.
기존 사람이 하던 업무를 빅데이터를 기반으로 한 인공지능이 하게 되니 시간이 단축된 것이다.
예를 들어, 생산계획 단계에서 소Lot(최소 주문량에 미달하는 규모) 주문 처리에 드는 평균 시간이 12시간이었다. 그러나 인공지능이 자동으로 소Lot 주문을 판단하고 설계하는 데 걸리는 시간이 1시간으로 대폭 줄었다.
이는 포스코가 소Lot 주문에 영향을 주는 인자 12개를 도출해내고, 인공지능이 스스로 주문을 판단할 수 있도록 학습시켰기 때문이다. 주문 판단은 97%의 정확도를 보였고, 설계 사이즈를 맞추는 것도 99.9%의 정확도를 보였다. 원가 비용 절감에도 매우 효율적일 것으로 기대된다.
철광석이 용광로에 들어가기 전 소결 공정을 거치게 된다. 이는 균일한 크기와 성분의 소결광을 만드는 것이 핵심이다. 철광석과 코크스의 경우, 알맹이가 작아 육안으로 확인하기도 어려울 정도다. 이렇다 보니 사람이 하게 되면 숙련도와 노하우에 따라 소결광의 품질이 달라지는 단점이 있다.
이 과정을 인공지능이 데이터를 기반으로 딥 러닝을 통해 스스로 실시간 제어할 수 있게 되면서 조업 편차는 60% 개선됐다. 또한 3%에 달하는 연료비도 절감됐는데, 이를 연 단위로 환산하면 약 19억 원의 비용 절감 효과가 나타난다.
출하 단계에서도 연 5억 원의 물류비 절감 효과도 기대할 수 있다.
‘AI 배선 시스템’을 구축해 선박이 항구에서 기다리는 시간을 최소화하고, 목적지에 따라 포항과 광양 중 어디서 생산해야 물류비를 절감할 수 있는지도 인공지능이 판단해, 물류비를 줄일 수 있다.
포스코는 포스프레임을 중소기업 등 비즈니스 파트너와 함께 공유하고 있다.
포스프레임을 적용한 대표기업 중 하나가 ‘동국산업’이다.
포스코가 동국산업으로 열연재를 공급할 때마다, 소재에 이물질이 어느 부분에 어느 정도 있는지를 예측한 데이터를 포스프레임을 통해 제공한다.
이 데이터는 동국산업의 ‘최적 산세 AI’로 넘어간다. 인공지능은 데이터를 바탕으로 최적값을 뽑아내 산세 처리를 한다. 이후 결과 데이터는 포스프레임으로 넘어간다.
이 과정이 여러 번 반복되면서, 빅데이터가 포스프레임에 쌓인다. 인공지능은 이러한 반복 학습을 거쳐 고도화되면서 최적화된 제품을 생산할 수 있게 된다.
포스코는 중견기업과 더불어 중소기업을 위한 스마트팩토리 컨설팅에도 집중하고 있다.
포스코는 중소벤처기업부와 공동으로 추진하는 ‘상생형 스마트공장 구축지원’ 사업으로 작년까지 110개 기업에 스마트팩토리를 구축했다.
동시에 ‘스마트 역량 강화 컨설팅’도 패키지로 제공해 포스코 고유의 현장 혁신 기법인 ‘QSS’를 통한 선진적 현장 노하우도 전수하고 있다. 포스코는 2023년까지 200억 원을 출연해 총 1000개의 기업이 스마트팩토리를 구축할 수 있도록 지원할 방침이다.
정은경 기자 ek7869@fntimes.com
가장 핫한 경제 소식! 한국금융신문의 ‘추천뉴스’를 받아보세요~
데일리 금융경제뉴스 Copyright ⓒ 한국금융신문 & FNTIMES.com
저작권법에 의거 상업적 목적의 무단 전재, 복사, 배포 금지