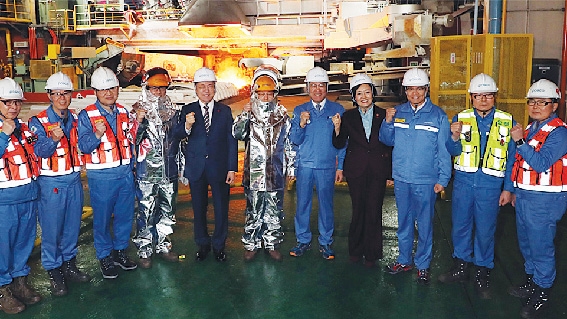
최정우닫기
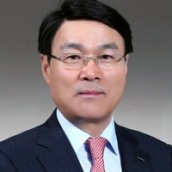
◇ 스마트팩토리 통해 생산 효율성 UP
포스코는 지난해 세계경제포럼으로부터 등대공장으로 선정됐다. 철강산업에서 생산성 향상을 위해 AI 기술을 적용하는 등 4차 산업혁명의 핵심기술을 적극 도입해 세계 제조업의 미래를 혁신적으로 이끌고 있다는 이유에서다.
포스프레임으로 전 공장의 데이터를 수집하고, 정형화해 스스로 최적의 공정 조건을 내놓고, 공장을 제어할 수 있게 됐다. 포스코는 스마트팩토리 실현을 앞당길 수 있었다.
포스코는 12시간 걸리던 ‘소Lot’ 주문 처리를 AI가 1시간으로 줄였다. 소Lot란 최소 주문량에 미달되어 생산상 제약을 받는 주문을 일컫는다.
2제강공장은 전로부터 연주까지 타이밍과 온도, 성분을 제어하는 통합 제어 시스템(PTX)을 개발했다.
용선의 온도와 성분, 원료 조건에 맞게 AI가 학습하도록 설계하여 온도 적중률을 80%에서 90%로 올렸으며, 원료 사용량도 60% 줄였다. 표면 품질 예측 모델도 개발하여 불필요한 검사가 없어져 연간 약 6억원 이상의 원가절감 효과가 기대된다.
후판 평탄도는 최적 조건을 생성하여 제품 교정률을 50% 저감하면서 연간 약 13억원을 절약할 수 있게 됐다.
포스코는 2016년부터 2019년까지 스마트팩토리 구축을 위해 321건의 과제를 수행하면서 총 2520억원의 원가절감 효과를 거뒀다.
◇ 중소기업과 ‘상생형’ 스마트 혁신 확대에 앞장
포스코는 중소벤처기업부와 ‘상생형 스마트공장 구축 지원 및 스마트화 역량강화 컨설팅’ 사업을 추진 중이다. 오는 2023년까지 총 200억원을 출연해 1000개 기업을 지원할 예정이다. 포스코는 지난해 총 110개 기업에 ‘상생형 스마트공장’을 구축했다.
또한 ‘스마트화 역량강화 컨설팅’도 제공해, 포스코의 현장 혁신 기법인 ‘QSS(Quick Six Sigma)’를 통한 선진적 현장 노하우를 전수했다.
중소기업과의 스마트팩토리 프로젝트에서 가장 큰 성과는 QR코드를 활용한 수리품 공정관리로 꼽혔다.
관리자들은 현장에 직접 가지 않아도 QR코드를 인식해 입고 일자와 수리 범위, 출고일자 등 제품의 상태를 실시간으로 파악할 수 있다.
성과측정 완료된 기업 대상 조사 결과, 스마트사업이 적용된 설비와 공정에서 생산성과 품질이 각각 43%와 52% 증가하고, 비용과 납기는 27% 가량 줄어는 것으로 나타났다.
상생형 스마트공장 참여 중소기업인 동국산업과 종합폴스타 경우 표면처리 최적조건 도출 AI제어모델과 모바일 공정관리 체제를 통해 생산성과 매출이 각각 60%와 35%가 증가했다.
최정우 회장은 2020년 신년사를 통해 기업시민 공생가치 창출을 경영이념 구현의 핵심 중 하나로 꼽았다.
포스코의 혁신 역량과 스마트팩토리 경험을 중소기업과 공유하고 지원하는 등 산업 생태계 경쟁력을 제고해 나가겠다는 방침이다.
또한 AI 기반의 스마트 팩토리를 확산하여 글로벌 One POSCO, One Quality 생산체제로 진일보해 벤처플랫폼을 활용한 장기 육성 사업 발굴에도 나설 계획이다.
김경찬 기자 kkch@fntimes.com
가장 핫한 경제 소식! 한국금융신문의 ‘추천뉴스’를 받아보세요~
데일리 금융경제뉴스 Copyright ⓒ 한국금융신문 & FNTIMES.com
저작권법에 의거 상업적 목적의 무단 전재, 복사, 배포 금지